Regular maintenance and timely repairs of a concrete parking lot are essential to ensure its longevity and functional performance. As concrete surfaces are constantly exposed to various weather conditions and vehicular traffic, they are susceptible to damage such as cracks, spalling, and surface deterioration. Unattended issues can lead to more severe structural damage over time, potentially resulting in costly repairs and safety hazards. This guide will explore how to repair concrete parking lot, providing practical advice to help maintain its integrity and appearance.
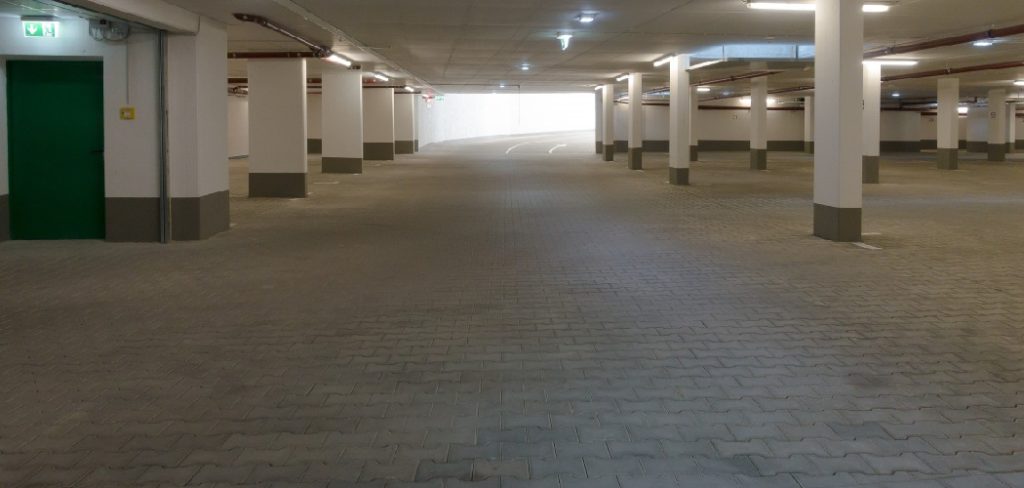
Importance of Maintaining Concrete Parking Lots
Maintaining a concrete parking lot is paramount for several reasons. First and foremost, it ensures the safety of pedestrians and vehicles. Properly maintained surfaces minimize the risk of accidents caused by tripping or vehicular damage from potholes and uneven pavement. Additionally, regular maintenance helps to preserve the aesthetic appeal of the property, which can positively influence customer perception and business reputation.
From a financial perspective, consistent upkeep is a cost-effective strategy, as it extends the lifespan of the pavement and reduces the likelihood of expensive overhaul repairs. Lastly, well-maintained parking lots are environmentally beneficial, as timely repairs prevent pollutants from entering the drainage system due to surface material breakdown.
Understanding Common Issues in Concrete Parking Lots
Concrete parking lots, while durable, are not immune to various issues that can arise over time. One of the most common problems is cracking, which can result from factors such as temperature fluctuations, heavy loads, or inadequate initial construction. Small cracks, if left untreated, can expand and lead to more significant structural concerns. Spalling, another frequent issue, involves the chipping or flaking of the concrete surface, often caused by freeze-thaw cycles or the use of deicing chemicals.
Additionally, surface deterioration like scaling or discoloration can occur due to weather exposure and improper finishing practices. Understanding these common issues is crucial for implementing effective maintenance strategies, thereby preserving the structural integrity and visual appeal of concrete parking lots.
10 Methods How to Repair Concrete Parking Lot
1. Crack Sealing
Crack sealing is one of the most common and essential methods for repairing minor cracks in concrete parking lots. Over time, small cracks can form due to temperature changes, freeze-thaw cycles, or heavy loads. If left unattended, these cracks can widen and deepen, allowing water to penetrate and cause further damage. Crack sealing involves cleaning the crack thoroughly, removing debris and dust, and then filling it with a flexible sealant that prevents water infiltration. This method is cost-effective and can significantly extend the life of the parking lot by preventing more severe damage.
2. Pothole Patching
Potholes form when moisture penetrates small cracks in the concrete and weakens the underlying base. As vehicles pass over these weak spots, the concrete can break apart, leading to potholes. Patching potholes is an essential repair method for maintaining a smooth and safe parking lot surface. The repair process involves cleaning out the loose debris and broken pieces of concrete from the pothole and then filling the void with a patching compound, such as asphalt or concrete mix. Compacting the material ensures that the patch is level with the surrounding surface and can withstand traffic.
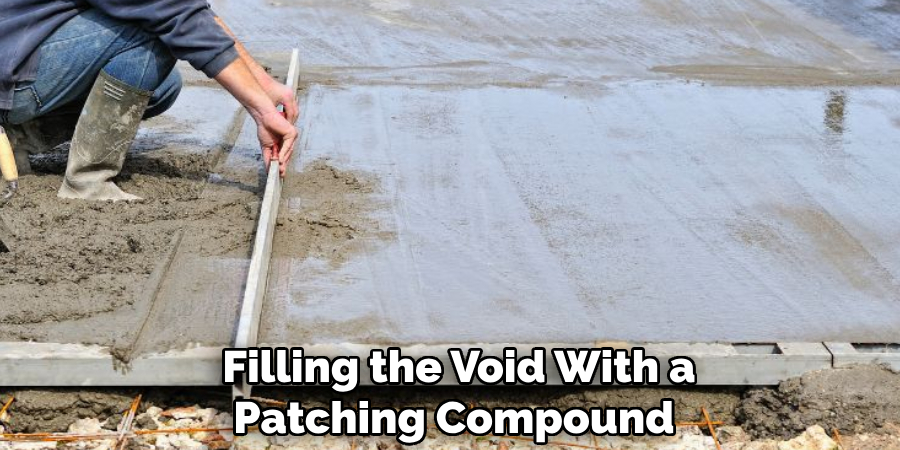
3. Full-Depth Concrete Patching
For more severe cases of concrete damage where the integrity of the slab is compromised, full-depth concrete patching may be required. This method involves removing the damaged section of the concrete entirely, down to the base material. After the damaged section is cleared, a fresh layer of concrete is poured to fill the space, creating a strong and durable repair. Full-depth patching is typically used for large cracks, deep spalling, or areas where the concrete is significantly weakened. Although it is more labor-intensive than other methods, it provides a long-lasting solution for major repairs.
4. Surface Grinding and Smoothing
Surface grinding is an effective method for addressing minor unevenness or surface-level damage on a concrete parking lot. Over time, the surface of the concrete may develop minor bumps, cracks, or rough patches due to wear and tear. Grinding the surface smooth with specialized equipment removes these imperfections, improving both the appearance and safety of the parking lot. After grinding, the surface is left level and smooth, which reduces the risk of tripping hazards and prevents further deterioration caused by uneven wear.
5. Slab Jacking (Mudjacking)
Slab jacking, also known as mudjacking, is a technique used to lift and level sunken or uneven concrete slabs. Over time, the ground beneath a concrete parking lot can shift or settle due to poor compaction, water infiltration, or soil erosion. When this happens, sections of the parking lot may sink, creating an uneven surface that can pose safety risks. Slab jacking involves drilling small holes into the sunken slab and injecting a slurry mixture of cement, sand, and water underneath the slab to lift it back to its original position. This method restores the level surface without the need for extensive removal or replacement.
6. Concrete Resurfacing
If a parking lot’s surface has widespread damage, but the underlying structure is still sound, concrete resurfacing can be an effective repair method. Resurfacing involves applying a thin overlay of new concrete over the existing surface to cover minor cracks, spalling, and surface wear. The new layer bonds with the old concrete, creating a smooth, fresh surface.
In addition to improving the appearance of the parking lot, resurfacing can also enhance its durability and resistance to future wear. This method is often more cost-effective than complete replacement and can add several years to the life of the parking lot.
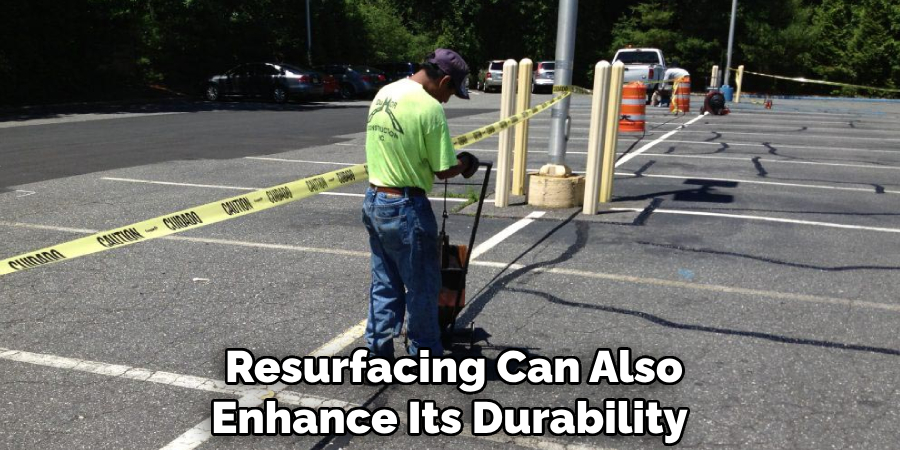
7. Joint Repair and Sealing
Concrete parking lots have expansion joints that allow for movement and prevent cracking as the concrete expands and contracts with temperature changes. Over time, these joints can deteriorate or become filled with debris, causing them to lose their effectiveness. Joint repair involves cleaning out the joints and applying a fresh sealant to restore their flexibility and prevent water from seeping into the cracks between slabs. Sealing the joints also prevents vegetation growth and the accumulation of dirt and debris, which can contribute to further damage.
8. Epoxy Injection for Crack Repair
For structural cracks that extend deep into the concrete, epoxy injection is a highly effective repair method. Epoxy injections involve filling the crack with a two-part epoxy resin that bonds the concrete back together, restoring its strength and preventing the crack from expanding further. This method is particularly useful for vertical or diagonal cracks that are caused by shifting or settling of the concrete. Epoxy injections provide a long-lasting repair that reinforces the structural integrity of the parking lot and prevents water infiltration.
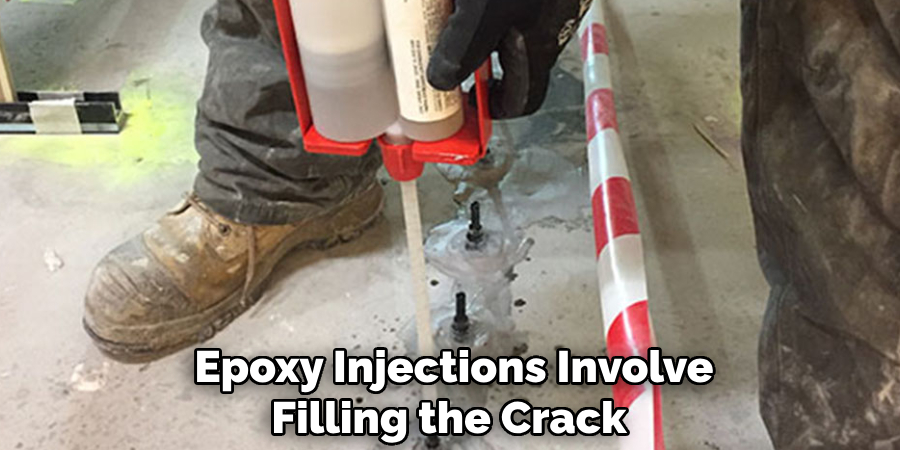
9. Concrete Spall Repair
Spalling occurs when the surface of the concrete flakes or peels away, leaving rough, uneven patches that can become hazardous or unsightly. Spalling is often caused by freeze-thaw cycles or improper concrete mixing during installation. To repair spalled areas, the damaged concrete is first removed, and the surface is cleaned to ensure proper adhesion. A resurfacing compound, such as a cementitious overlay, is then applied to fill in the spalled area and create a smooth, level surface. Spall repair restores both the appearance and functionality of the parking lot, preventing further deterioration.
10. Preventative Maintenance and Sealing
Preventative maintenance is key to avoiding major repairs in a concrete parking lot. Regularly inspecting the surface for signs of wear, cracks, or damage allows you to address minor issues before they become severe. Applying a concrete sealant periodically can protect the surface from moisture, chemicals, and abrasion. Sealants form a protective layer on the surface of the concrete, reducing the risk of cracks, spalling, and other forms of deterioration. Sealcoating also enhances the appearance of the parking lot by providing a clean, smooth finish and helps extend the life of the concrete.
Things to Consider When Choosing a Repair Method
When selecting the most appropriate repair method for a concrete parking lot, there are several important factors to consider. First, assess the extent and type of damage present. For example, minor surface issues may be addressed effectively with surface grinding or resurfacing, while deeper structural damage may necessitate full-depth patching or epoxy injection.
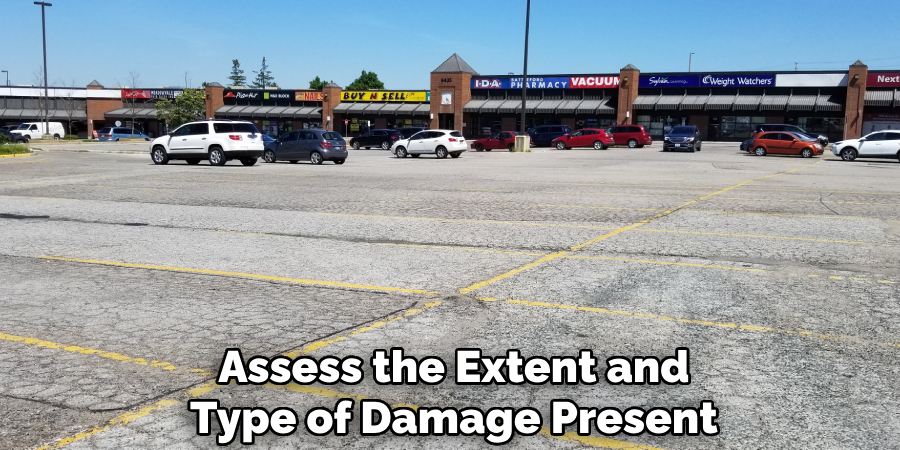
The frequency and volume of traffic on the parking lot also influence the repair choice, as areas that experience heavy use may require more robust solutions to ensure long-lasting results. Additionally, budget constraints play a critical role in decision-making, and it’s essential to balance cost with the effectiveness and durability of the selected method.
Conclusion
Maintaining the integrity and longevity of a concrete parking lot is essential for safety, functionality, and aesthetics. Implementing effective repair methods like full-depth patching, surface grinding, and epoxy injection can address specific types of damage while preserving the structure’s durability. Proactive approaches such as regular inspections and preventative maintenance can mitigate the need for more extensive repairs by catching early signs of wear and damage. Thanks for reading, and we hope this has given you some inspiration on how to repair concrete parking lot!