Constructing a warehouse can be a daunting task, involving numerous considerations and decisions. However, the benefits of having your own warehouse for storage and distribution far outweigh these challenges. Below are some of the main reasons why you should learn to construct a warehouse.
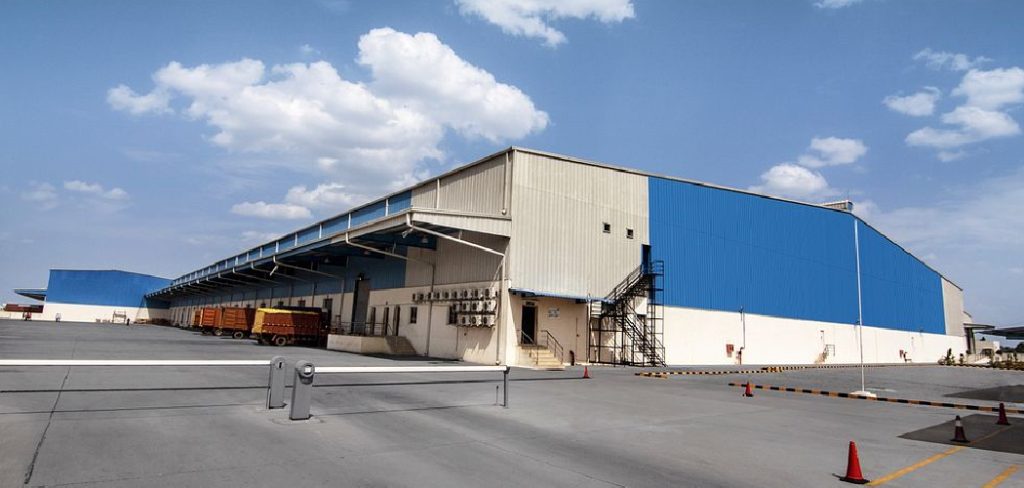
The main advantage of constructing a warehouse is having a dedicated space for storage and distribution of goods. Having your own warehouse eliminates the need to rely on third-party logistics providers or rented storage facilities. This means you have complete control over the organization and flow of your inventory, leading to increased efficiency in managing your supply chain. You can find step-by-step instructions on how to construct a warehouse in this blog article.
Materials You Will Need
- Measuring Tape
- Hammer
- Nails
- Screwdriver
- Drill
- Screws
- Level
- Stud Finder
- Pencil
- Safety Goggles
When it comes to home improvement projects, having the right tools and materials is essential. While the specific materials you will need will depend on the project itself, there are some basic materials that every DIY enthusiast should have on hand.
Step-by-step Instructions for How to Construct a Warehouse
Step 1: Inspect the Site
Before constructing a warehouse, it is important to thoroughly inspect the site where the warehouse will be built. Take note of any potential hazards or obstacles that may need to be addressed during construction.
Step 2: Develop a Plan and Budget
Create a detailed plan for your warehouse project, including a budget that outlines all necessary materials, labor costs, and timelines. This will help ensure that the project stays on track and within budget.
Before beginning construction, it is crucial to obtain all necessary permits and approvals from local authorities. This may include building permits, zoning approvals, and environmental clearances.
Step 3: Prepare the Foundation
The foundation of a warehouse is critical for its structural integrity and stability. This step involves excavating the site, pouring a concrete slab, and laying out the necessary plumbing and electrical systems.
Once the foundation is in place, it is time to begin assembling the framework of the warehouse. This includes erecting steel beams or wooden frames according to the construction plan.
Step 4: Install Roofing and Walls
After the framework is complete, it is time to install the roofing and walls. This step may involve using prefabricated panels or constructing the walls on-site. Doors and windows are important for ventilation, natural light, and access in a warehouse. Decide on their placement during the planning phase and install them during this step.
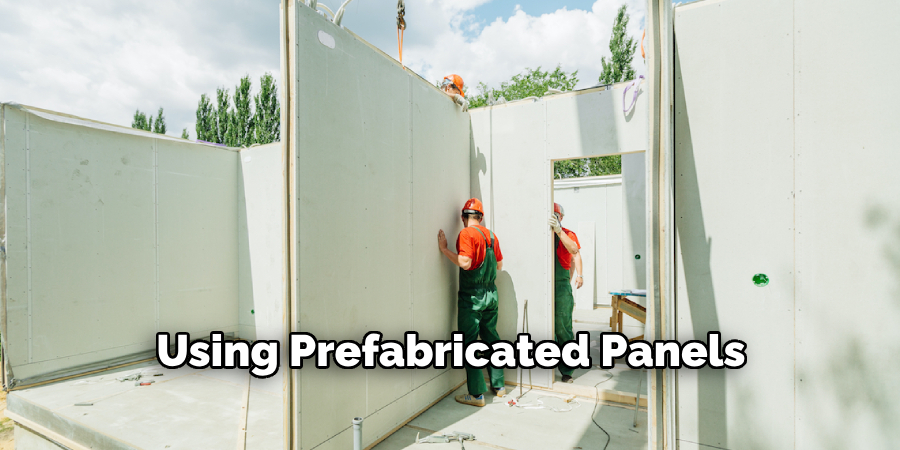
Step 5: Install Utilities
The next step is to install all necessary utilities such as plumbing, electrical wiring, and HVAC systems. These systems are essential for the functioning of a warehouse.
Once all major construction is complete, it is time to add finishing touches to both the interior and exterior of the warehouse. This may include painting, flooring, and landscaping.
Step 6: Final Inspection and Approval
Before the warehouse can be put into use, it must undergo a final inspection to ensure that all construction meets building codes and regulations.
Once approved, the warehouse is ready for operation.
By following these steps, you can construct a warehouse that is safe, functional, and within budget. Remember to always have a detailed plan in place and obtain all necessary approvals before beginning construction. Keeping these steps in mind will help ensure a successful warehouse project from start to finish.
Safety Tips for How to Construct a Warehouse
- Always wear appropriate safety gear such as hard hats, steel-toed boots, and high-visibility vests while on the construction site.
- Make sure all workers are properly trained and follow safety protocols at all times. This includes using equipment correctly and adhering to proper lifting techniques.
- Conduct regular safety meetings and inspections to identify potential hazards and address them promptly.
- Keep the work area clean and organized to prevent slips, trips, and falls. This includes proper storage of materials and debris removal.
- Follow all safety regulations and building codes to ensure the structural integrity of the warehouse.
- Have a first aid kit readily available on-site in case of any accidents or injuries.
- In case of extreme weather conditions, take necessary precautions and protect workers from potential hazards. This may include temporary shelter, proper clothing, and limiting work hours during extreme heat or cold.
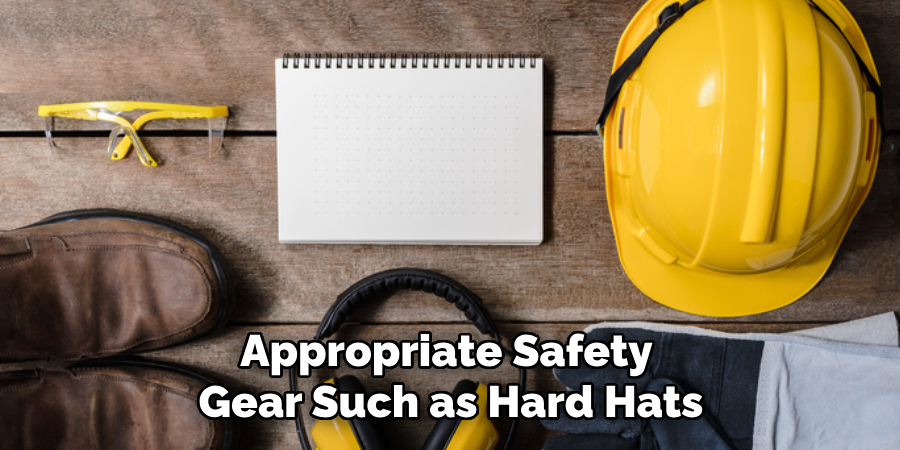
By following these safety tips, you can minimize the risk of accidents and ensure a safe construction process for your warehouse project. Remember to prioritize safety at all times for the well-being of yourself and others on the job site.
Environmentally Friendly Options for Constructing a Warehouse
- Use Sustainable Materials: When constructing a warehouse, it is important to consider the materials being used. Opt for sustainable and environmentally friendly options such as recycled steel or bamboo instead of traditional concrete or wood.
- Install Energy-efficient Systems: From lighting to heating and cooling, there are many energy-efficient systems available for warehouses. These not only help reduce environmental impact but can also save on operational costs in the long run.
- Implement a Rainwater Harvesting System: Instead of relying solely on municipal water, implement a rainwater harvesting system to collect and use rainwater for various purposes within the warehouse. This can significantly reduce water usage and help conserve this precious resource.
- Incorporate Natural Lighting: When designing the layout of the warehouse, consider incorporating natural lighting through skylights or windows. This not only reduces the need for artificial lighting but also provides a more pleasant working environment for employees.
- Utilize Green Roofing: Green roofs, which are covered with plants, can help reduce energy consumption by providing insulation and absorbing heat. They also aid in stormwater management, reduce air pollution, and provide a habitat for wildlife.
- Install Solar Panels: Another way to reduce energy consumption is by installing solar panels on the roof of the warehouse. This renewable energy source can help power various systems and equipment, further reducing the carbon footprint of the warehouse.
- Promote Recycling and Waste Reduction: Implementing a recycling program in the warehouse can greatly reduce waste sent to landfills. Additionally, finding ways to minimize packaging materials and repurpose materials can also greatly reduce the environmental impact of warehouse operations.
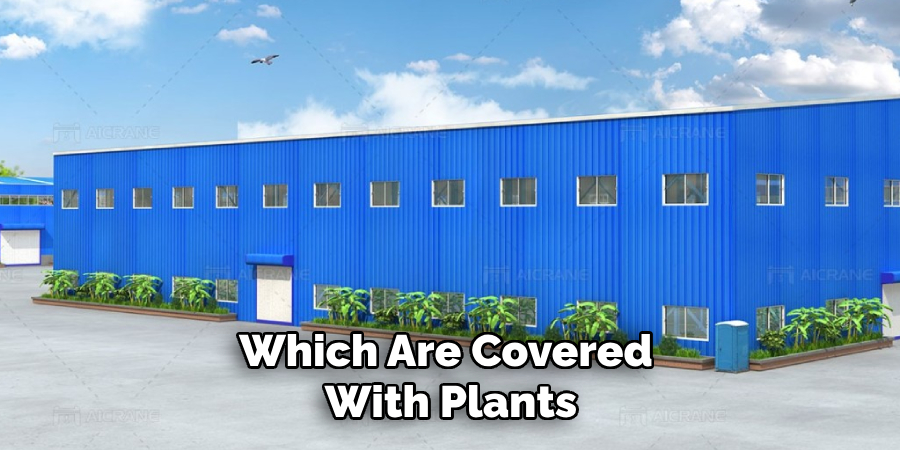
These are just a few environmentally friendly options for constructing a warehouse. It is important for businesses to prioritize sustainability and consider the long-term impact of their construction choices.
Factors Should Be Considered When Choosing a Location for a Warehouse
1. Accessibility
The first factor to consider when choosing a location for a warehouse is accessibility. This includes both the ease of transportation and proximity to major transportation routes such as highways, railroads, and ports. A well-connected location can significantly reduce shipping costs and improve delivery times.
2. Cost
Cost is also an important consideration when selecting a warehouse location. Factors such as rent, utilities, and taxes should be carefully evaluated to ensure that the overall cost of operating a warehouse in a particular location is feasible for your business.
3. Labor Force Availability
The availability of a skilled labor force is crucial when deciding on a warehouse location. It is important to consider factors such as unemployment rates, education levels, and specific skills required for your industry. A location with a large pool of potential employees can ensure smooth operations and reduce training costs.
4. Proximity to Suppliers
The proximity to suppliers is another vital factor in the selection process. A warehouse located near your suppliers can help minimize transportation costs, improve inventory management, and reduce lead times.
5. Customer Base
Understanding the location of your target customer base is crucial when choosing a warehouse location. A location that is close to your customers can significantly reduce shipping costs and improve customer satisfaction by ensuring timely deliveries.
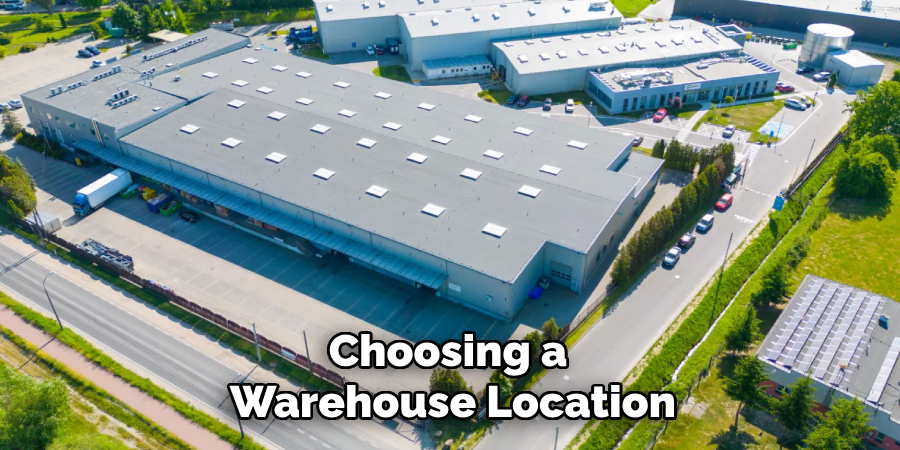
6. Infrastructure
The infrastructure of a potential warehouse location should also be evaluated carefully. This includes the condition of roads, utilities, and access to high-speed internet. A well-developed infrastructure can ensure efficient operations and minimize disruptions.
7. Zoning and Regulations
Before finalizing a warehouse location, it is essential to consider zoning regulations and other local laws. These can significantly impact the cost of operating in a particular area, so it is important to thoroughly research and understand them before making a decision.
When choosing a warehouse location, it is crucial to find a balance between these factors based on your business needs. For example, a warehouse near a major port may be ideal for businesses that import and export goods, but it may not be cost-effective for businesses with a primarily local customer base.
Common Mistakes to Avoid When Constructing a Warehouse
1. Lack of Proper Planning
One of the most common mistakes in warehouse construction is starting without a well-thought-out plan. This can lead to inefficient use of space, poor traffic flow, and other issues that can negatively impact operations.
2. Not Considering Future Needs
Another mistake is not taking into account future growth and expansion when constructing a warehouse. It is essential to plan for potential changes in your business and leave room for expansion or reconfiguration of the warehouse.
3. Ignoring Safety Measures
Safety should always be a top priority when constructing a warehouse. Failing to implement proper safety measures can lead to accidents and injuries, as well as legal issues that can significantly impact your business.
4. Poor Use of Space
Efficient use of space is crucial in a warehouse. Failing to optimize the layout and organization of your warehouse can result in wasted space, which can lead to higher operating costs.
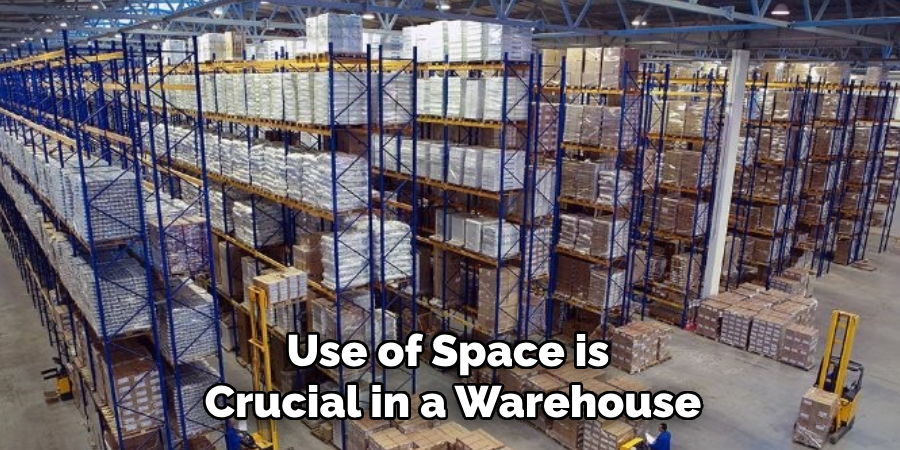
5. Inadequate Lighting
Lighting plays a significant role in warehouse operations, as it impacts visibility and safety. Not having enough lighting or using poor quality lighting can lead to mistakes, accidents, and reduced productivity.
6. Lack of Flexibility
A warehouse that is not designed with flexibility in mind can create limitations for your business as it grows and evolves. It is important to consider the use of adjustable storage systems and other features that can adapt to changing needs.
7. Cutting Corners on Construction Materials
Choosing low-quality materials or cutting corners during construction may seem like a cost-saving measure, but it can end up costing more in the long run. It is important to invest in durable and high-quality materials to ensure the longevity and efficiency of your warehouse.
Avoiding these common mistakes can help you construct a functional, efficient, and cost-effective warehouse that meets your business needs both now and in the future. It is essential to carefully consider all aspects of warehouse construction and seek professional guidance when necessary to avoid costly errors.
Budget-friendly Options for Constructing a Warehouse
1. Renting
One budget-friendly option for constructing a warehouse is to rent an existing space. This can be a cost-effective solution for businesses that do not require a large amount of storage space or have limited funds for construction.
2. Modular Construction
Modular construction involves building components off-site and assembling them on-site, reducing labor and materials costs. It is also a faster construction method, allowing businesses to start operations sooner.
3. Renovating Existing Space
Renovating an existing building or space can be a more affordable option than constructing a new warehouse from scratch. This is especially beneficial for businesses that do not require specialized features or have limited space and budget constraints.
4. Pre-engineered Buildings
Pre-engineered buildings are designed and manufactured off-site, then assembled on-site. This can save time and money compared to traditional construction methods.
5. Used Equipment
Another way to save on warehouse construction costs is by purchasing used equipment instead of new. This includes shelving, forklifts, and other storage solutions that can be found at discounted prices.
6. Energy-efficient Features
Investing in energy-efficient features, such as LED lighting and insulation, can help reduce long-term operating costs for your warehouse. This may require a higher upfront investment but can result in significant savings over time.
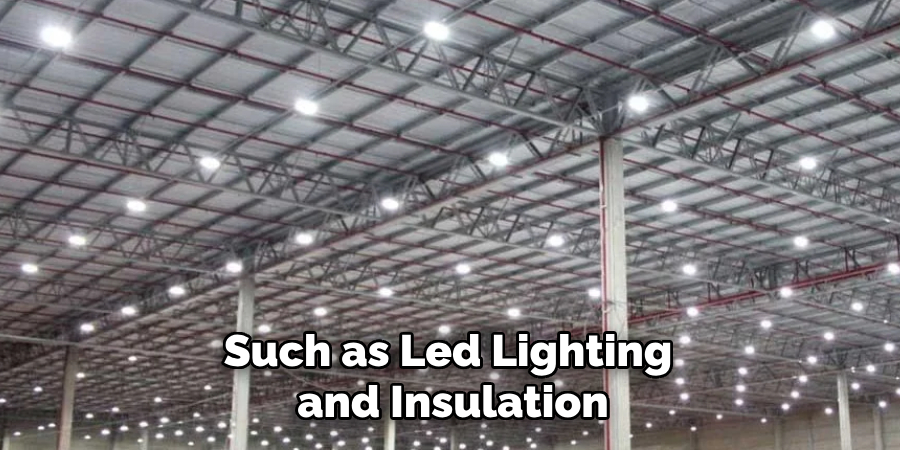
7. Negotiating with Contractors
When working with contractors, it is important to negotiate prices and explore different options to find the most cost-effective solution for your warehouse construction. It never hurts to ask for discounts or explore alternative materials and methods.
By considering these budget-friendly options, businesses can construct a warehouse that meets their needs without breaking the bank. It is important to carefully compare costs and potential long-term savings when choosing the best construction option for your business.
What Are Some Design Considerations When Planning the Layout of a Warehouse?
- Maximizing Storage Space: One of the most important design considerations when planning a warehouse layout is how to maximize storage space. This can be achieved by utilizing vertical space and implementing efficient shelving systems.
- Efficient Traffic Flow: Another crucial consideration is designing the warehouse layout in a way that promotes efficient traffic flow. This means strategically placing aisles, loading docks, and inventory locations to minimize travel time and optimize movement of goods.
- Accessibility: A well-designed warehouse layout should also prioritize accessibility. This means ensuring that all areas of the warehouse are easily reachable, especially for large equipment such as forklifts or pallet jacks.
- Safety Measures: The safety of workers and the inventory itself is a top priority when designing a warehouse layout. This includes implementing proper fire exits, emergency equipment, and designated walkways to prevent accidents and facilitate safe movement of goods.
- Flexibility: Warehouse layouts should be designed with flexibility in mind. This means leaving room for expansion or reconfiguration as the business grows or changes over time.
- Integration of Technology: With advancements in technology, it is important to consider how technology can be integrated into the warehouse layout. This can include automated systems for inventory tracking, picking and packing, and even utilization of drones for efficient storage and retrieval.
- Environmental Factors: Another consideration is how environmental factors may impact the warehouse layout. This includes proper ventilation, lighting, temperature control, and protection against potential hazards such as flooding or extreme weather conditions.
- Cost Efficiency: Ultimately, a well-designed warehouse layout should also prioritize cost efficiency. This means finding the balance between maximizing storage space, promoting efficient traffic flow, and implementing technology while keeping costs manageable.
- Continuous Evaluation: It is important to continuously evaluate and reassess the warehouse layout to identify any potential areas for improvement or inefficiencies. This can help ensure that the warehouse continues to operate at optimal levels and adapt to changing business needs.
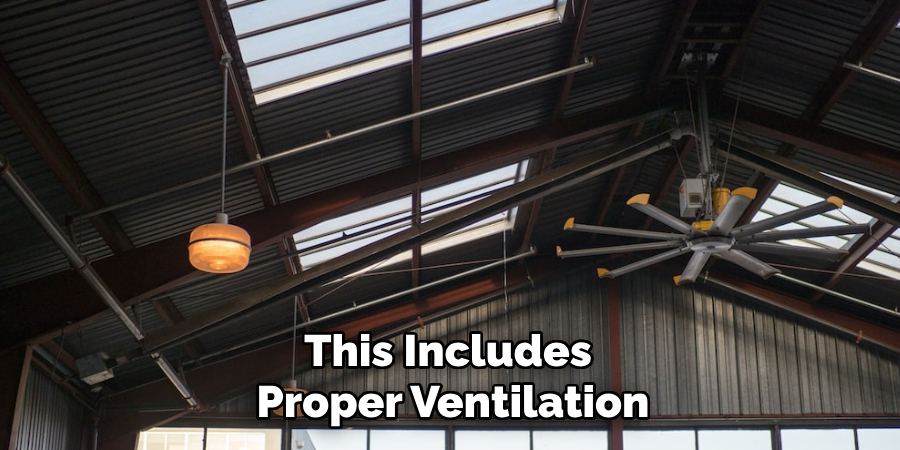
By considering these design considerations when planning the layout of a warehouse, businesses can create an efficient and safe environment for storing and moving goods. It is important to prioritize storage space, traffic flow, accessibility, safety measures, flexibility, technology integration, environmental factors, cost efficiency, and continuous evaluation in order to optimize operations and meet customer demands.
Conclusion
In conclusion, constructing a warehouse requires careful planning, budgeting, and execution. It is not a simple task and should not be taken lightly. A poorly constructed warehouse can lead to significant financial losses for a company.
To successfully construct a warehouse, it is important to consider factors such as location, size, layout, storage capacity, accessibility, and safety regulations. These factors will determine the efficiency and functionality of the warehouse in the long run.
Another important aspect to consider is the materials used for construction. It is crucial to choose high-quality, durable materials that can withstand the weight and pressure of heavy storage. Investing in quality materials may incur a higher initial cost, but it will save money in the long run by reducing maintenance and repair costs.
I hope this article has been beneficial for learning how to construct a warehouse. Make Sure the precautionary measures are followed chronologically.